LASER CUT ANTISPATTER FLUID
Quit spattering around
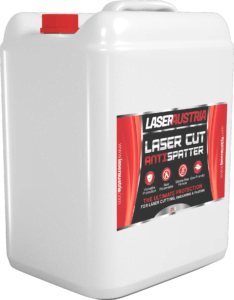
LASER CUT ANTISPATTER FLUID
Superior Protection for Laser Operations
Elevate your laser cutting and welding processes with LASER CUT ANTISPATTER FLUID, engineered for excellence:
- Advanced Surface Protection:
Safeguards sheet metal panels, pipes, profiles, and equipment from spatter and slag, ensuring your projects remain pristine. - Universal Metal Compatibility:
Effectively protects a wide range of metal surfaces including steel, stainless steel, and aluminum, offering flexibility across various applications. - Eco-Friendly and Safe:
Free from silicone and non-flammable, this biodegradable formula promotes a safer and more environmentally conscious workspace.
Transform your laser cutting and welding with
LASER CUT ANTISPATTER FLUID – the smart choice for cleaner, safer, and more efficient operations.